« A part is not just a specification and a price but a story that is built up between customer and supplier. This partnership can only be successful if it is based on mutual trust, transparence and technical background. » Damien AGUESSE, DECOREC CEO.
Discover below the different steps of how we can support you in bar-turning and grinding.

Examination of your project
- Technical discussion
- Commercial proposition
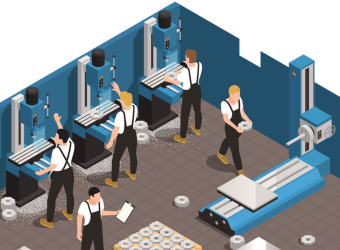
Industrialisation review
- Project launch review
- Production implementation and review
- Planning of tasks

Production and series life
- Production
- Customer relations management
- Process optimisation
1 – Examination of your project
- Understand the needs and issues involved in consultation of the part to be done
- Technical discussions between the different design offices and planning departments in order to optimize the technical-economic aspect of the part:
- Feasibility study and proposals for improvement
- Global approach depending on the part’s environment and industrial constraints
- Suggestions for alternative materials
- Simulation in fluid mechanics or materials
- Submission and validation of a commercial proposition
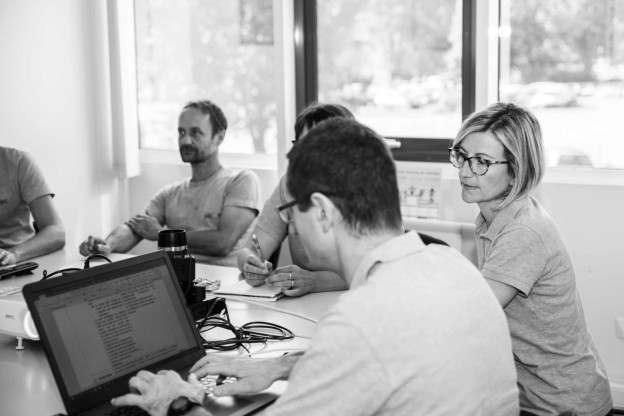
2 – Industrialisation review
This concerns the production of new parts, also known as first order review. When the process is run-in we go directly into series production mode.
- Industrialisation review
- Project launch review with a team from all departments: management, technical, sales, quality, supply chain, sales admin, production and planning
- Production implementation
- Production process validation
- Feedback following launch of the series
- Planning of the industrialisation follow-up tasks, along with the review
- Delivered with schedules for the customer
- Twice-weekly industrialisation review follow-up
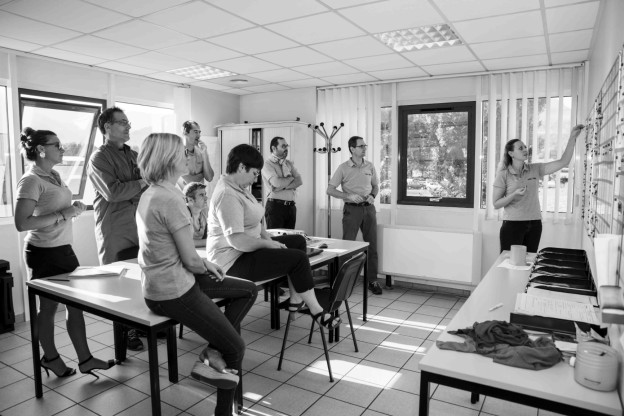
3 – Production and series life
For every first order, initial samples are made and put to the customer for approval.
- Production:
- Bar-turning on ESCOMATIC lathes (Ø 2 to 9), single-spindle NC (Ø 4 to 51), multi-spindle cam controlled or NC (Ø 8 to 35)
- Centreless grinding in-feed and plunge, lapping
- Milling: special machines developed by our design office
- Finishing: sand-blasting, shot-peening
- Sorting: special machines developed by our design office
- Assembling
- Packing
- Preparation of initial samples
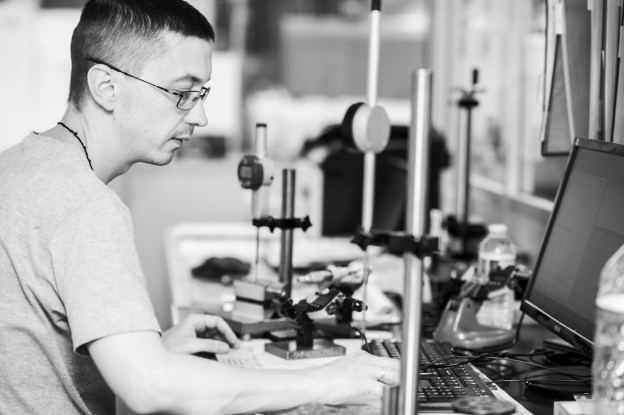
Customer relations management
- Analysis and taking into account the forecast,
- Inventory given to the customer,
- Proposals for productivity gains,
- Price control with revision depending on raw materials rates,
- Regular face-to-face or video-call updates,
- Mesure of customer satisfaction through interactive survey
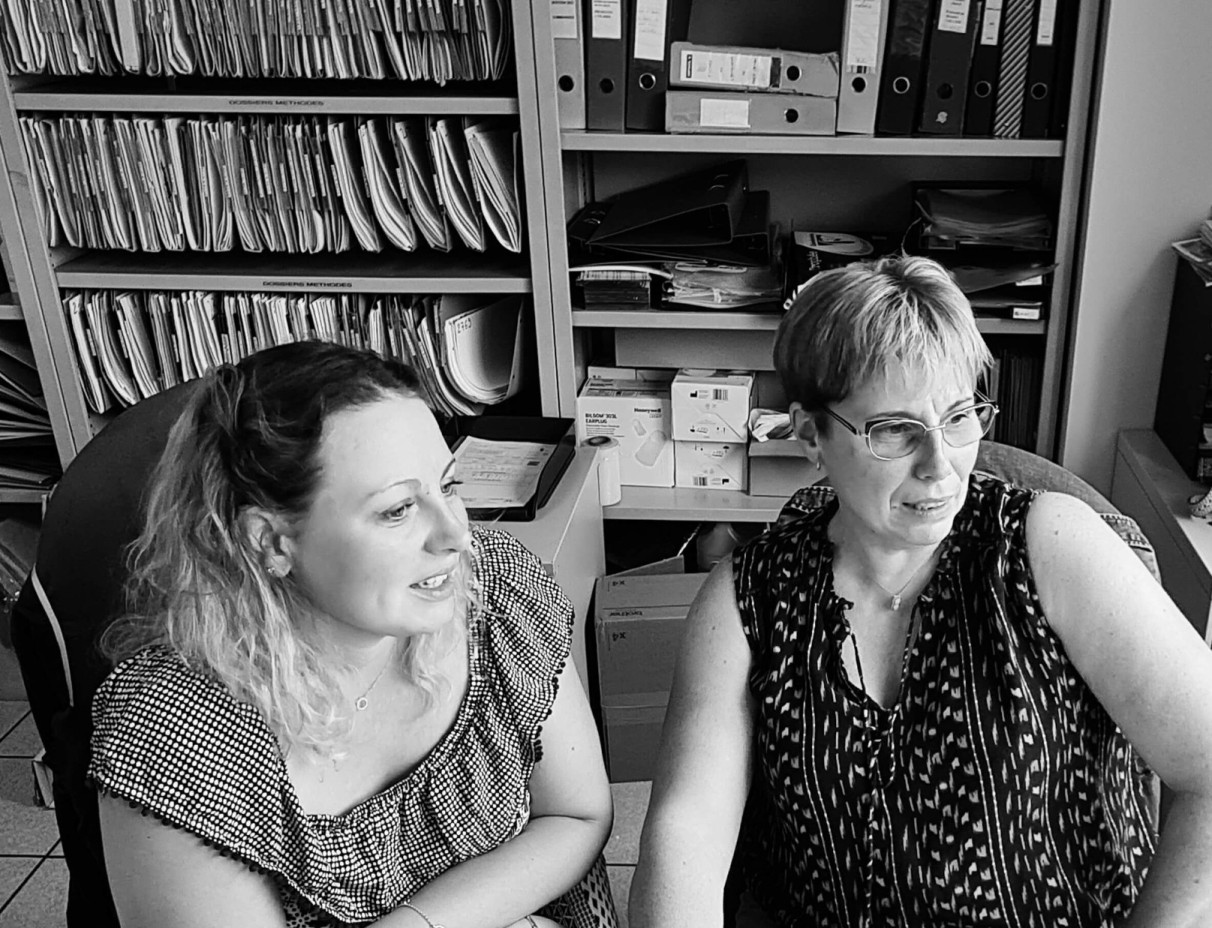
… via extranet portals
- Order and forecast transmisssion.
- Pick-up request.
- Logistics paperwork: ASN.
- Sending of invoices and payment follow-up.
- Quality documents on-line: PPAP.
Process optimisation
- Ability to develop our own machines to meet customers’ capability needs.
- Find productivity gains.
Tracabilty
- Ensured throughout the process thanks to a patented system which reduces handling of the tracability files.
Inspections
Done at all process steps: setting-up, production, returns from sub-contracting and final inspection.
Discuss together your projects
Our control of the complete value chain allows us to improve our responsiveness and ensure better cost control. We respect the criteria of cleanliness thanks to our high-performance equipment : specific cleaning machines, particule extractors. We have inspection and measuring devices to ensure the conformity of the parts.